Downtime is a key metric in turbine performance. It is, perhaps, one of those indicators that brings wind asset managers, IT ops, and O&M teams on the same page. All with one objective: how to combat downtime on wind farms? Our answer: With dedicated wind turbine asset management software.
Turbine availability is a crucial aspect of wind farm operation. It asserts that asset management and O&M teams must ensure that when wind is blowing, turbines are in the perfect condition to generate power. It’s an essential wind energy key performance indicator to keep an eye on.
Moreover, minimizing downtime is part of the equation that has driven down the levelized cost of energy produced at wind farms. The International Renewable Energy Agency (IRENA) predicts that between 2015 and 2025, the cost of wind power will fall by more than 26%.
Hence, turbine uptime and availability has far reaching affects. It dictates the profitability of this clean energy source, and the stability of a nation’s grid.
Simply put, it’s mission-critical.
3 Ways Wind Turbine Asset Management Software Helps Deal with Downtime
Aside from the technical O&M jobs, smart wind turbine asset management software can also help keep downtime low. A platform that acts as a central hub of all information can make it easier to flag trouble areas and questionable downtime patterns.
How so? Let’s talk about three ways a wind turbine asset management software sets up a fleet for maximum productivity.
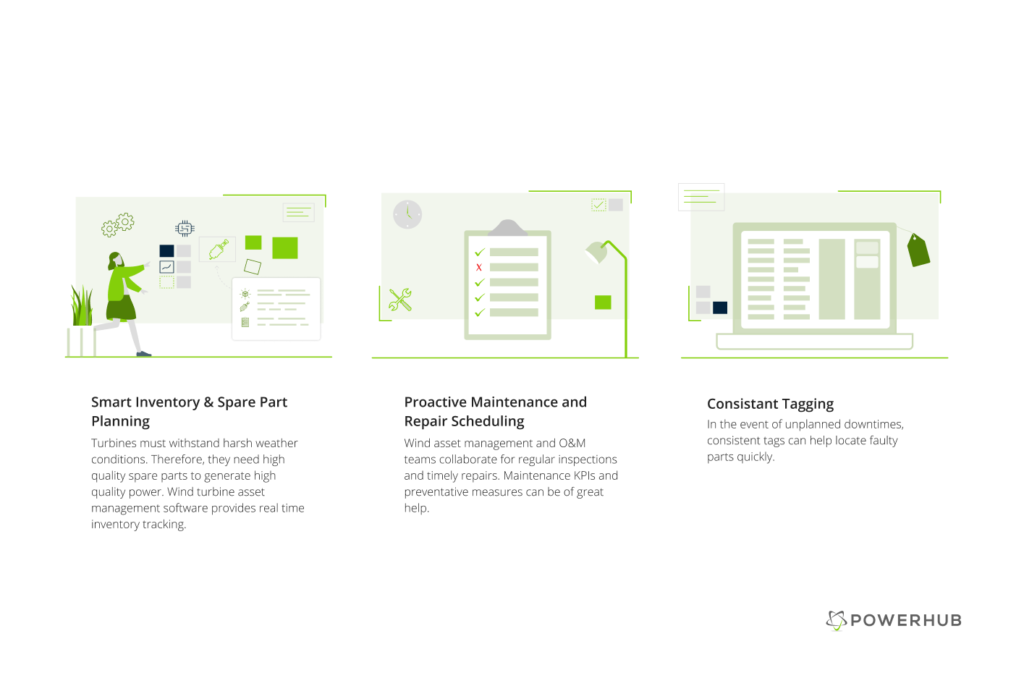
Smart Inventory & Spare Part Planning
Everyone talks about the proliferation of wind energy in the renewables mix. However, very few shed light on the fact that as this power source grew in popularity, so did the need for robust inventory and spare part planning.
While turbines are constructed to withstand harsh weather conditions, they need high-quality spare parts to generate high-quality power. And being out of these parts can translate into losses worth millions of dollars for insurance companies.
Therefore, real-time inventory tracking is no longer optional. And wind turbine asset management software provides just that. It equips asset managers with automated spare part scheduling, contract compliance, and supplier invoicing. As a result, they save time – and most of all keep turbines up and running.
Proactive Maintenance and Repair Scheduling
This is where turbine asset management and O&M teams’ collaboration comes into play. Important indicators include; regular inspections, timely repairs, and maintenance cycle efficiency.
They will either point to a proactive maintenance schedule – one that is tracked within a wind turbine asset management software – or one that is clogged with overtime jobs. We’ve previously talked in great detail about the maintenance KPIs successful wind asset management is built on.
Preventative repair scheduling is, perhaps, one of the easiest ways to ensure maximum uptime for a fleet.
Consistent Tagging
Turbine parts and components have unique tags. Mounted atop mammoth towers, these components are not too easy to access. This is why RFID tags help. A consistent tagging system is a signature feature of a dedicated wind turbine asset management software.
In the event of unplanned downtimes, consistent tags can help locate faulty parts quickly. Moreover, tags also help share performance and operational information between teams, making downtime analysis so much easier.
How Well Are You Combating Downtime?
When we talk about combating downtime, an important factor – apart from technical issues – we really stress on is the motivation and attitude of asset management and O&M teams.
These internal stakeholders are closest to the wind turbines, and hence, their attitudes towards performance and production are of prime importance.
In this regard, a dedicated wind turbine asset management software helps with more than simply tactical management. It helps streamline the assessment process for these teams and adds value to their work. Instead of manually recording performance, working with a wind turbine asset management software like PowerHub automates and visualizes everyday workflows.
The result? Well, you’ll see for yourself: mission combat downtime – accomplished.